Strategi Peningkatan Kapasitas Gudang untuk Mendukung Pengiriman Kargo Udara
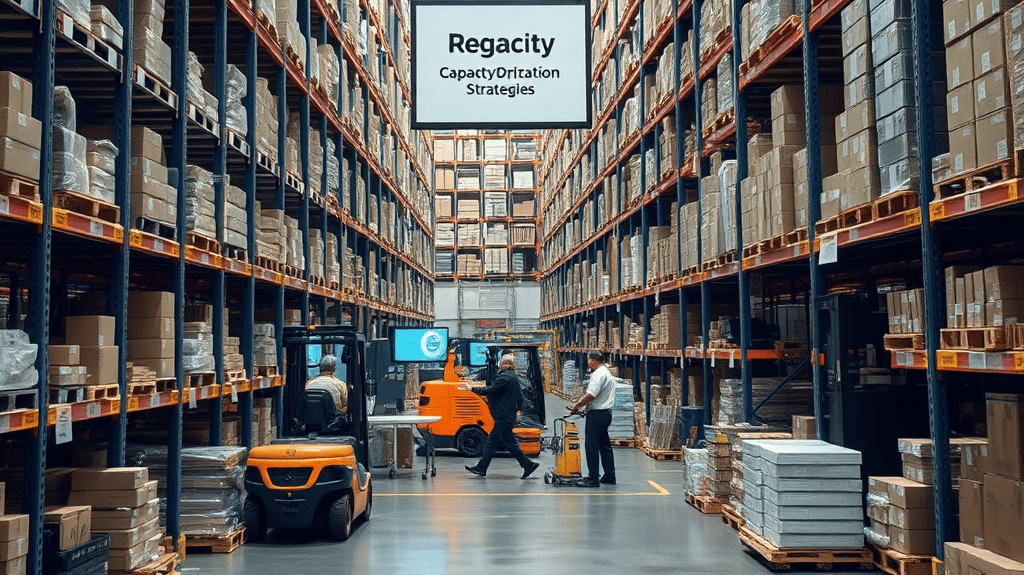
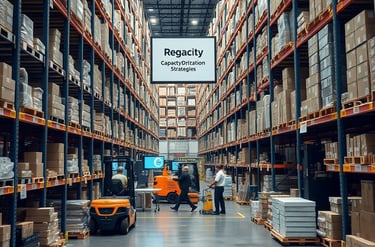
Meningkatkan kapasitas gudang adalah langkah krusial bagi perusahaan logistik dan kargo udara yang ingin mempertahankan keunggulan kompetitif serta memastikan kelancaran rantai pasok.
1. Analisis Kebutuhan dan Proyeksi Volume Kargo
Sebelum merencanakan penambahan ruang atau peralatan baru, langkah pertama adalah melakukan analisis kebutuhan secara menyeluruh. Tim manajemen gudang wajib mengumpulkan data historis volume kargo, tren musiman, hingga proyeksi pertumbuhan setidaknya untuk 12–24 bulan mendatang.
Pengumpulan Data Historis: Telaah laporan bulanan dan tahunan untuk mengidentifikasi periode puncak dan sepi. Informasi ini akan membantu menyusun model perencanaan kapasitas yang realistis, meminimalkan risiko underutilization ataupun bottleneck.
Proyeksi Pertumbuhan: Gunakan data order masuk dari klien korporat, tren ekspor-impor, dan rencana ekspansi rute udara. Rencana pertumbuhan harus disertai angka proyeksi minimum, optimis, dan ekstrem, sehingga strategi yang dikembangkan dapat fleksibel merespon berbagai skenario.
Identifikasi Kebutuhan Khusus: Beberapa jenis kargo, seperti bahan farmasi berpendingin atau barang berbahaya, memerlukan ruang tersendiri. Pisahkan data volume berdasarkan suhu dan kategori bahaya untuk memastikan alokasi ruang sesuai standar keselamatan.
Dengan fondasi analisis ini, perusahaan dapat merancang kapasitas gudang tidak berdasarkan dugaan, melainkan data konkret yang mendasari setiap keputusan investasi.
2. Optimalisasi Tata Letak (Layout) dan Alur Kerja
Setelah mengetahui berapa banyak ruang yang dibutuhkan, fokus berikutnya adalah mengatur ulang tata letak gudang agar alur kerja maksimal, mengurangi waktu penanganan, dan meminimalkan perjalanan internal.
Pembagian Zona Fungsional: Bentuk zona penerimaan (receiving), penyimpanan (storage), pengemasan ulang (repacking), dan pengiriman (dispatch) dengan batasan jelas. Zona penyimpanan harus terdekat dengan area muat pesawat untuk menghemat waktu bongkar-muat.
Koridor dan Akses: Perlebar lorong utama minimal 3–4 meter agar forklift dan pallet jack dapat melewati dengan lancar. Tandai jalur kendaraan dengan cat reflektif untuk menambah keselamatan saat operasional malam hari.
Penentuan Lokasi Barang Cepat Gerak: Terapkan prinsip ABC analysis, dimana barang dengan perputaran tinggi (kategori A) diletakkan paling dekat pintu keluar. Barang kategori C, yang jarang bergerak, dapat ditempatkan di rak lebih tinggi atau area yang lebih jauh.
Flow Visual Management: Pasang papan informasi atau layar digital di area utama untuk memonitor status stok real-time dan grafik alur keluar masuk barang. Informasi ini membantu supervisor segera mengambil keputusan if terjadi backlog atau kelebihan volume.
Dengan tata letak yang disesuaikan, proses penanganan kargo berlangsung lebih mulus, mengurangi waktu tunggu pesawat, dan memaksimalkan pemanfaatan ruang.
3. Peningkatan Kapasitas Penyimpanan
Untuk mengakomodasi volume kargo yang terus meningkat, perusahaan perlu menambah kapasitas fisik dan memaksimalkan penggunaan ruang vertikal.
Rak Pallet Multi-Tier: Implementasikan sistem rak bertingkat (multi-tier pallet racking) dengan ketinggian menyesuaikan plafon gudang, memanfaatkan ruang vertikal. Jangan lupa memperhitungkan beban muatan maksimum per rak serta biaya instalasi lift kecil untuk akses rak tinggi.
Mezzanine Floor: Bangun mezzanine di area gudang untuk menciptakan tingkat lantai tambahan. Lantai mezzanine cocok untuk menyimpan barang dengan permintaan musiman atau cadangan, sementara lantai utama tetap untuk stok reguler.
Modular Storage System: Gunakan rak geser atau mobile racking yang dapat digeser otomatis untuk menutup lorong saat tidak digunakan, sehingga ruang penyimpanan bisa lebih rapat tanpa koridor tetap lebar.
Pallet Flow Rack: Bagi kargo dengan perputaran cepat, rak jenis ini memanfaatkan gaya gravitasi untuk memindahkan pallet ke area pengambilan dengan lancar, mempercepat proses First-In-First-Out (FIFO).
Investasi dalam solusi penyimpanan modern menghadirkan peningkatan kapasitas signifikan sekaligus mempercepat proses keluar-masuk barang.
4. Automasi Proses Penanganan Barang
Meskipun istilah tertentu tidak disinggung, automasi tetap menjadi tulang punggung peningkatan produktivitas. Simak beberapa contoh penerapan teknologi mekanis yang memudahkan pekerjaan manual.
Conveyor Belt dan Roller Track: Jalur konveyor memindahkan paket dari area penerimaan ke penyortiran otomatis. Desain lintasan sesederhana mungkin, dengan kemiringan optimal agar paket tidak terjebak dan memerlukan campur tangan manual.
Automated Guided Vehicles (AGV): Robot pemindah tumpukan barang beroda dapat mengantarkan pallet dari zona penyimpanan ke area pengemasan. AGV yang terprogram rutenya mengurangi ketergantungan operator forklift, sekaligus meminimalkan risiko kecelakaan.
Sortation System: Mesin sortasi mampu memisahkan paket berdasarkan destinasi bandara, ukuran, atau prioritas. Setiap paket akan diarahkan lewat lengan geser (diverter) ke conveyor yang tepat, menghemat waktu proses sortir manual.
Penggunaan fasilitas mechanized handling menjadi langkah strategis menurunkan biaya operasional jangka panjang dan meningkatkan kecepatan throughput gudang.
5. Penguatan Sumber Daya Manusia
Gudang yang canggih akan sia-sia tanpa tim handal. Berinvestasi dalam pengembangan kompetensi karyawan mutlak dilakukan.
Pelatihan Sertifikasi: Adakan pelatihan bersertifikat ULD handling, keamanan kargo berbahaya, serta prosedur bea cukai. Karyawan dengan sertifikat lebih siap menghadapi inspeksi dan prosedur kompleks.
Cross-Training: Setiap karyawan perlu memahami lebih dari satu fungsi, misalnya petugas penerimaan juga mahir di mesin sortation, sehingga saat ada kekosongan mendadak dapat langsung diisi tanpa mengganggu alur kerja.
Tim Shift Berbasis Beban Kerja: Analisis beban operasional per jam dan sesuaikan jadwal shift agar puncak aktivitas selalu terisi tenaga memadai tanpa overstaffing saat periode sepi.
Program Kesejahteraan dan Insentif: Tawarkan bonus berdasarkan metrik kinerja, seperti waktu siklus penanganan, akurasi inventaris, dan tingkat insiden. Karyawan termotivasi menjaga kualitas kerja demi bonus tambahan.
Pengembangan SDM memupuk budaya tanggung jawab, meningkatkan produktivitas, dan menekan angka kesalahan operasional.
6. Peningkatan Sistem Manajemen Inventaris
Sistem manajemen inventaris yang akurat meminimalkan kelebihan stok ataupun kekurangan ruang.
Real-Time Inventory Tracking: Gunakan sistem berbasis barcode/QR yang mencatat setiap gerakan. Setiap penerimaan, pemindahan, atau pengeluaran barang otomatis tercatat, memudahkan audit internal kapan saja.
Forecasting dan Reorder Point: Implementasikan algoritma dasar untuk menghitung reorder point berdasarkan lead time dan safety stock. Dengan demikian, gudang tidak kehabisan ruang karena penumpukan barang tanpa perencanaan.
Cycle Counting: Lakukan perhitungan stok sebagian (cycle count) setiap minggu pada zona berbeda. Proses ini lebih ringan dibanding stock opname penuh, namun tetap menjaga akurasi data melebihi 99%.
Dengan data inventaris yang transparan, manajer gudang dapat mengambil keputusan cepat saat menghadapi lonjakan volume mendadak.
7. Kolaborasi dengan Pihak Eksternal dan Mitra
Tidak semua investasi harus dilakukan secara mandiri. Kerja sama strategis bisa membuka akses ke fasilitas skuplai lebih besar.
Third-Party Logistics (3PL) Provider: Alihkan sebagian kapasitas penyimpanan ke gudang 3PL saat puncak musim liburan. 3PL biasanya memiliki infrastruktur luas dan pengalaman operasional yang matang.
Shared Warehouse: Beberapa perusahaan kargo menawarkan sistem gudang bersama (shared warehouse) yang biaya operasionalnya dibagi berdasarkan ruang yang dipakai. Cocok bagi usaha skala menengah yang tidak memerlukan gudang eksklusif sepanjang tahun.
Transit Hub Regional: Jika volume melimpah, buka hub transit di kota lain yang terhubung ke bandara internasional. Barang dapat dikonsolidasi di hub regional sebelum diangkut ke gudang utama di bandara.
Melalui kolaborasi, perusahaan bisa scale up capacity secara fleksibel tanpa beban investasi penuh, sekaligus memanfaatkan jaringan partner untuk efisiensi biaya.
8. Standarisasi Prosedur dan Audit Berkala
Kapasitas besar saja tidak cukup tanpa prosedur yang seragam dan audit yang konsisten.
Standard Operating Procedures (SOP): Buat petunjuk tertulis untuk setiap aktivitas—mulai penerimaan, penyimpanan, hingga pengiriman. SOP harus mudah dipahami, dilengkapi ilustrasi, dan di-review minimal setahun sekali.
Key Performance Indicators (KPI): Tetapkan indikator seperti waktu siklus (cycle time), tingkat akurasi inventaris, dan biaya per unit. Pantau KPI setiap bulan dan bahas dalam rapat tim untuk perbaikan berkelanjutan.
Internal Audit dan Inspeksi: Terapkan audit mendadak oleh tim Quality Assurance. Cek kesesuaian prosedur, kondisi fisik gudang, dan kelengkapan alat keselamatan seperti APAR (alat pemadam api ringkas).
Standarisasi dan audit menciptakan disiplin operasional, menurunkan risiko kesalahan, dan memastikan kapasitas yang ditambah benar-benar efektif.
9. Pengelolaan Risiko dan Kontinjensi
Pertumbuhan kapasitas mengandung potensi risiko baru. Perusahaan harus siap dengan rencana kontinjensi.
Asuransi Kargo dan Infrastruktur: Proteksi terhadap kebakaran, banjir, atau kerusakan mekanis. Pastikan polis mencakup nilai total aset gudang dan barang di dalamnya.
Sistem Cadangan Energi: Generator dan UPS (Uninterruptible Power Supply) harus tersedia untuk menjaga pendingin ruang beku dan operasi alat mekanis saat listrik padam.
Rencana Evakuasi dan Pemulihan: Latihan rutin untuk evakuasi gudang jika terjadi kebakaran atau bencana alam. Document recovery plan untuk inventaris dan sistem IT agar dapat pulih dalam waktu singkat.
Dengan persiapan risiko matang, peningkatan kapasitas jadi tidak menimbulkan beban baru saat keadaan tak terduga.
10. Evaluasi dan Perbaikan Berkelanjutan
Tahap akhirnya adalah meninjau hasil implementasi strategi dan terus menerus memperbaiki.
Review Periodik: Jadwalkan evaluasi setiap enam bulan untuk memeriksa apakah kapasitas gudang sudah memenuhi target volume dan KPI.
Feedback dan Inovasi: Ajak tim frontline memberikan masukan tentang kendala operasional sehari-hari. Data lapangan sering kali menjadi sumber ide peningkatan terkini.
Pilot Project Perbaikan: Sebelum meluncurkan perubahan besar, jalankan pilot di satu zona gudang untuk mengukur efektivitas, lalu skala ke seluruh area jika berhasil.
Dengan siklus Plan-Do-Check-Act, perusahaan logistik mampu menyesuaikan diri dengan dinamika volume kargo udara, selalu siap untuk tantangan berikutnya.
Kesimpulan
Meningkatkan kapasitas gudang untuk mendukung pengiriman udara bukan sekadar menambah luas lantai atau rak baru. Proses ini membutuhkan pendekatan menyeluruh: analisis data yang akurat, perancangan layout efisien, investasi pada sistem penyimpanan modern, automasi cerdas, pengembangan SDM, kolaborasi strategis, serta standar operasional tegas. Ditambah kesiapan mitigasi risiko dan evaluasi berkelanjutan, strategi ini akan mengantarkan perusahaan pada layanan kargo udara yang lincah, andal, dan siap tumbuh seiring peningkatan permintaan global.
Siap mengirimkan kargo udara Anda? Kirimkan melalui Hasta Buana Raya untuk solusi logistik yang andal dan aman!
👉 Hubungi 📱 +62-822-5840-1230 (WhatsApp/Telepon) untuk informasi lebih lanjut dan solusi pengiriman terbaik!
Digital Marketing
Kamis, 15 Mei 2025 10:00 WIB
Kami menyediakan layanan pengiriman udara yang aman, nyaman, dan terjangkau dari seluruh Indonesia. Layanan prioritas kami meliputi:
Pengiriman barang melalui udara (Pesawat Kargo, Sewa, dan Penerbangan Khusus)
Metode Pengiriman yang berbeda (Bandara ke Bandara , Gudang ke Gudang , dan Bandara ke Gudang)
Gudang dan Distribusi
Kontak
Bantuan
© 2024. Semua hak cipta dilindungi.
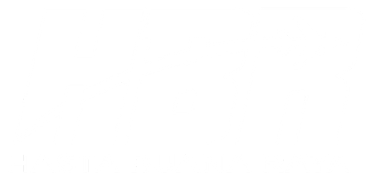
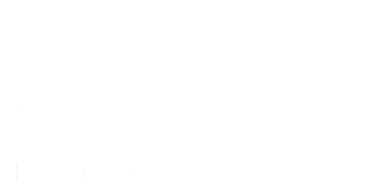
+62-811-9778-889
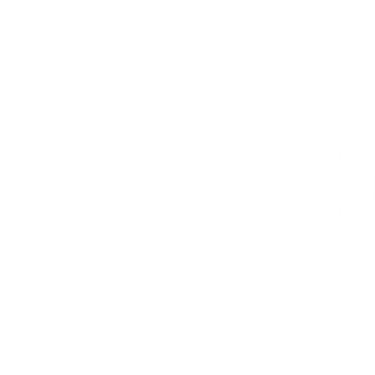
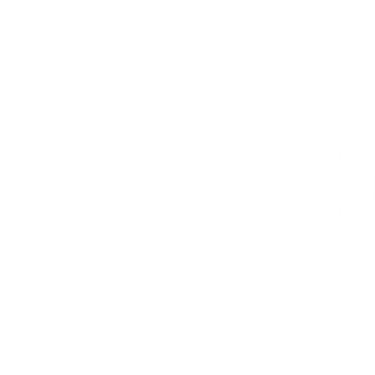
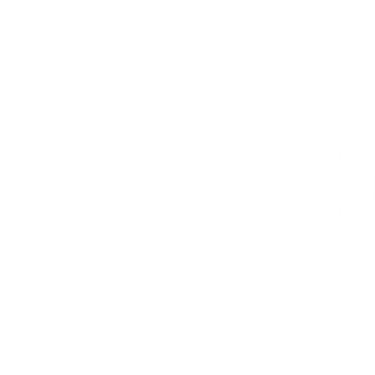
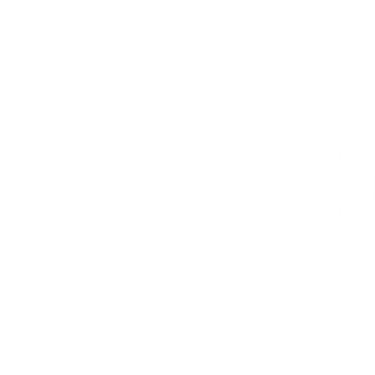
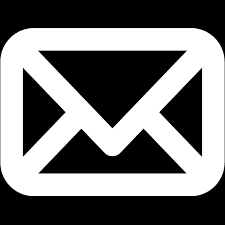
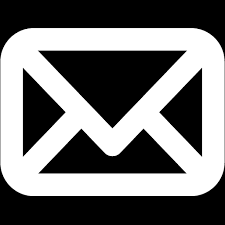